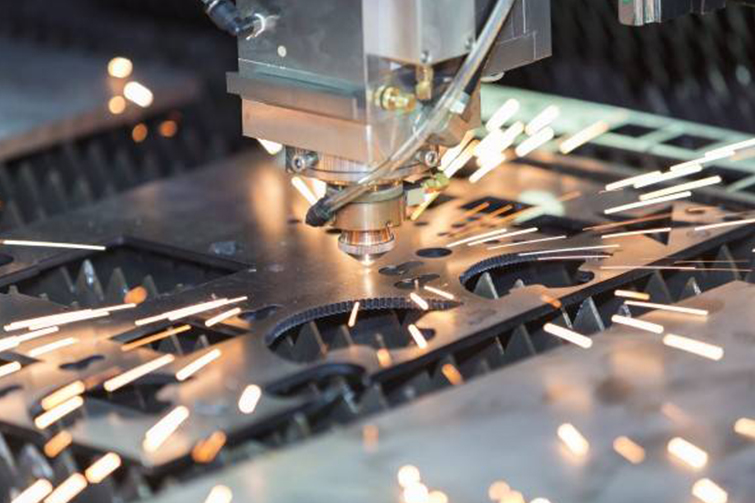
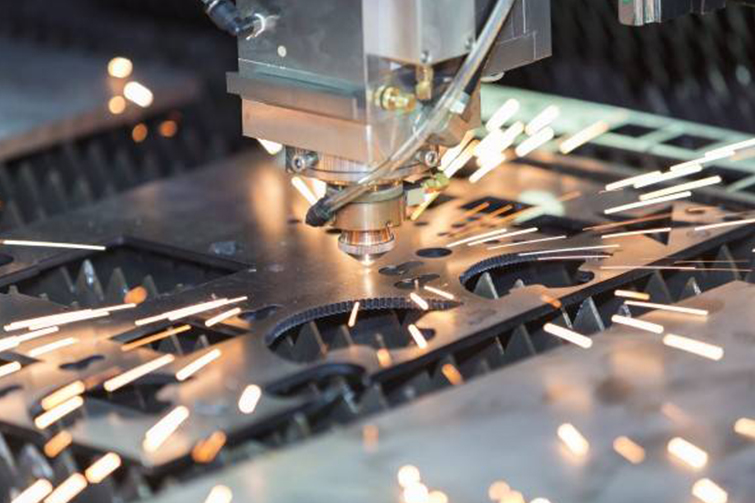
From 3D Prototype to Blueprint to Mass Production: A Comprehensive Guide
The journey from a 3D prototype to a finished product ready for mass production involves several critical stages. Each phase, from initial concept through prototyping, detailed design, and eventually to large-scale manufacturing, is essential in ensuring the final product meets quality, performance, and cost expectations. Below, we outline the key steps in this transformative process.
1. Conceptualization and Initial Design
Idea Generation:
- The process begins with an idea or a concept. This can be driven by market research, consumer feedback, technological advancements, or innovative thinking.
- Brainstorming sessions and sketching help in visualizing the product's form, function, and features.
Preliminary Design:
- Initial sketches and ideas are translated into digital designs using CAD (Computer-Aided Design) software. This helps in visualizing the product more precisely and allows for initial adjustments and refinements.
- Design considerations at this stage include the overall aesthetics, functional aspects, and how the product will be used by the end consumer.
2. 3D Prototyping
Creating a 3D Model:
- The CAD design is used to create a 3D model using 3D printing technology. This stage involves selecting the appropriate 3D printing method (e.g., FDM, SLA, SLS) based on the material and the level of detail required.
- The prototype serves as a tangible version of the digital model, allowing for a hands-on evaluation of the design.
Testing and Evaluation:
- The 3D prototype is evaluated for its design, functionality, and usability. This often involves physical testing to ensure the product meets the desired performance criteria.
- Feedback is gathered from stakeholders, which may include design teams, potential users, and engineers, to identify any improvements or modifications needed.
Iteration and Refinement:
- Based on the evaluation, the prototype is refined and reprinted as necessary. This iterative process continues until the design meets all the specified requirements.
- Prototyping is an essential phase where multiple iterations help in fine-tuning the product's design and function.
3. Blueprint and Detailed Design
Finalizing the Design:
- Once the prototype is approved, detailed design work is done to finalize the product's dimensions, materials, and other specifications.
- This includes creating detailed engineering drawings and documentation that will guide the manufacturing process.
Material Selection:
- Selecting the right materials is crucial for the product's performance, durability, and cost-effectiveness. This decision is based on factors like the product's intended use, environmental conditions, and regulatory requirements.
- Materials need to be sourced and tested to ensure they meet the required specifications.
Creating Manufacturing Drawings:
- Detailed blueprints and technical drawings are created, outlining every aspect of the product’s design. These drawings include dimensions, tolerances, and assembly instructions.
- The drawings must comply with industry standards and be clear enough to be used directly in the manufacturing process.
4. Tooling and Pre-Production Planning
Tooling Design and Development:
- Tools, molds, and dies necessary for mass production are designed and fabricated. This step is particularly critical for products that will be manufactured using methods like injection molding, casting, or stamping.
- The design of these tools must consider production efficiency, ease of use, and longevity.
Pilot Production Run:
- A pilot or small-scale production run is conducted to test the manufacturing process and the final product. This helps identify any potential issues with the design or the production line before full-scale production begins.
- The pilot run also provides an opportunity to make final adjustments to the product or the production process.
Supply Chain and Logistics Planning:
- Efficient supply chain management is crucial for ensuring that all materials and components are available when needed.
- Planning for logistics, storage, and distribution is also a key part of this stage to ensure smooth operations during mass production.
5. Mass Production
Setting Up the Production Line:
- The manufacturing facility is set up with the necessary equipment and machinery, as well as trained personnel, to begin mass production.
- The production line is optimized for efficiency, ensuring that the product can be produced at the desired volume and cost.
Quality Control and Assurance:
- Rigorous quality control measures are implemented to ensure that each unit produced meets the required standards. This includes regular inspections, testing, and adherence to quality management systems like ISO standards.
- Any deviations or defects are identified and rectified promptly to maintain product consistency and quality.
Scaling Up:
- Full-scale production is ramped up to meet market demand. This involves managing production schedules, maintaining supply chain fluidity, and ensuring continuous quality control.
- Scaling up also requires ongoing coordination between different departments and suppliers to handle increased production volumes efficiently.
6. Post-Production and Distribution
Packaging and Assembly:
- Products are assembled (if needed), packaged, and prepared for distribution. Packaging design plays a critical role in protecting the product and providing a good first impression to the customer.
- Automated packaging and assembly processes are often employed to maintain speed and consistency.
Distribution and Logistics:
- Efficient distribution strategies are implemented to get the product to retailers or directly to consumers. This involves coordinating with logistics providers and managing inventory levels.
- Effective logistics ensure that the product reaches the market on time and in good condition.
Market Launch and Sales:
- The final step is launching the product in the market. This includes marketing campaigns, sales strategies, and distribution to retail outlets or direct sales channels.
- Customer feedback is gathered post-launch to assess product performance and identify any areas for future improvement.
Conclusion
The journey from a 3D prototype to mass production is complex and involves meticulous planning and execution at each stage. It requires close collaboration among designers, engineers, and manufacturers to ensure that the final product meets all quality, performance, and cost objectives. Advances in 3D printing and digital design tools have significantly streamlined this process, making it more efficient and enabling faster time-to-market for new products.