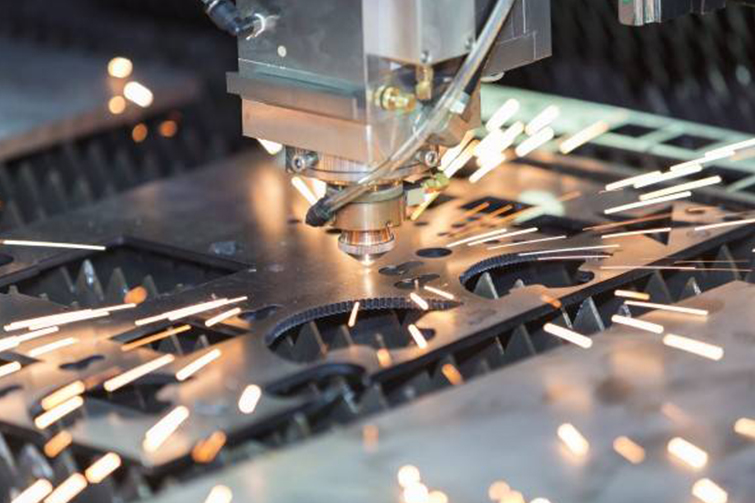
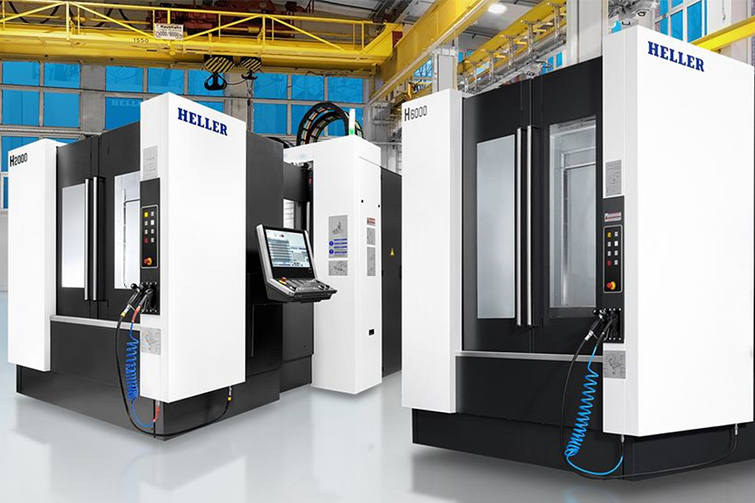
An Overview of Mold Processing Equipment
Mold processing is a critical aspect of modern manufacturing, playing a pivotal role in producing precision components for a variety of industries, including automotive, electronics, medical devices, and consumer goods. To create high-quality molds, a range of specialized equipment is utilized. This article explores the key types of mold processing equipment and their functionalities.
1. CNC Machining Centers
CNC (Computer Numerical Control) Machining Centers are essential in mold processing due to their precision and versatility. These machines use computer-controlled commands to move cutting tools in multiple axes, enabling the creation of complex and intricate mold shapes. There are several types of CNC machining centers:
- Vertical Machining Centers (VMC): These machines have vertically oriented spindles and are ideal for tasks requiring high precision and surface finish, such as milling and drilling.
- Horizontal Machining Centers (HMC): With horizontally oriented spindles, these machines excel in tasks where chip removal and heat dissipation are crucial, making them suitable for larger molds.
- 5-Axis Machining Centers: Capable of moving cutting tools or the workpiece in five different axes simultaneously, these machines are used for creating highly complex mold geometries.
2. EDM (Electrical Discharge Machining)
EDM is a unique machining process that removes material from a workpiece by using electrical discharges or sparks. It is particularly effective for hard metals and intricate mold details. EDM equipment includes:
- Wire EDM: Uses a thin wire as an electrode to cut profiles in the workpiece. It is ideal for creating precise, complex shapes and tight tolerances in hard materials.
- Die-Sinking EDM: Utilizes a shaped electrode to create cavities in the workpiece. This is commonly used for producing detailed mold features and intricate cavities.
3. Injection Molding Machines
Injection Molding Machines are the backbone of plastic mold manufacturing. They melt plastic pellets and inject them into a mold cavity under high pressure. Key components of these machines include:
- Injection Unit: Heats and injects the plastic material into the mold.
- Clamping Unit: Holds the mold closed during injection and cools the molded part.
- Control System: Manages the machine’s operations, ensuring precise control over temperature, pressure, and timing.
4. Grinding Machines
Grinding Machines are used to achieve high surface finish and dimensional accuracy on mold surfaces. They employ abrasive wheels to remove small amounts of material. Types include:
- Surface Grinders: Used for flat surfaces, providing a smooth finish.
- Cylindrical Grinders: Suitable for round surfaces, ensuring precise dimensional control.
- Tool and Cutter Grinders: Used for sharpening and creating cutting tools, essential for maintaining the sharpness of mold-making tools.
5. Laser Cutting and Engraving Machines
Laser Cutting and Engraving Machines use high-powered lasers to cut or engrave materials with extreme precision. They are ideal for adding intricate designs or patterns to mold surfaces and for cutting materials like metal and plastic with high accuracy.
6. Milling Machines
Milling Machines remove material using rotary cutters. They are versatile and used for shaping and forming mold components. Different types include:
- Manual Milling Machines: Operated by hand, suitable for simpler tasks or prototyping.
- CNC Milling Machines: Computer-controlled, offering high precision and the ability to handle complex tasks.
7. 3D Printing and Additive Manufacturing
3D Printing and Additive Manufacturing technologies are increasingly used in mold making for prototyping and even producing mold components. These machines build parts layer by layer from digital models, allowing for rapid and cost-effective production of complex geometries.
8. Heat Treatment Furnaces
Heat Treatment Furnaces are used to enhance the material properties of molds through processes like hardening, annealing, and tempering. This treatment improves the durability and performance of molds, especially those used in high-stress applications.
9. Coordinate Measuring Machines (CMM)
Coordinate Measuring Machines (CMM) are used for precise measurement and inspection of mold components. They ensure that the mold dimensions meet the required specifications and tolerances.
Conclusion
The diverse range of equipment used in mold processing highlights the complexity and precision involved in creating high-quality molds. From CNC machining centers and EDM machines to injection molding machines and 3D printers, each piece of equipment plays a crucial role in the mold manufacturing process. As technology continues to advance, mold processing equipment will evolve, further enhancing the capabilities and efficiencies of this essential industry.
These tools not only facilitate the creation of intricate and precise molds but also ensure that molds meet the stringent quality standards required for modern manufacturing.